Expert filling for a versatile range
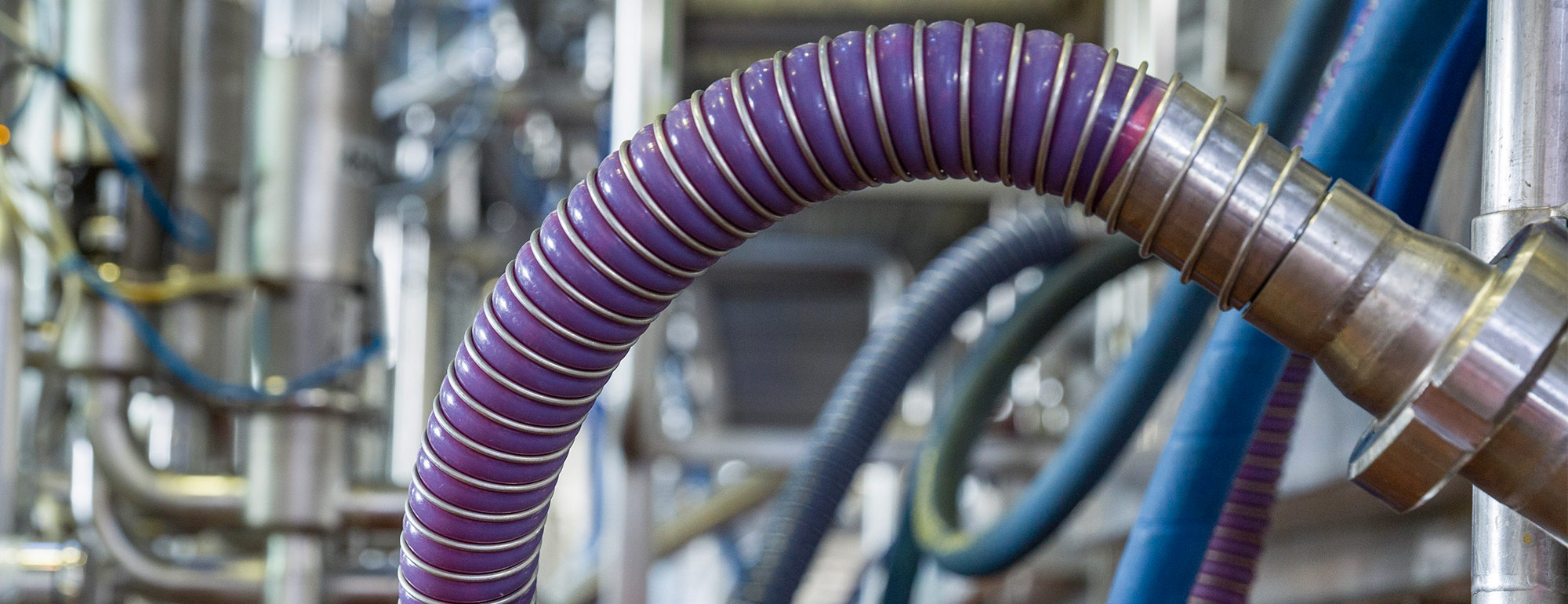
12.03.2024
But with cream please!
Chocolate pudding topped with cream, red jelly with vanilla sauce, yoghurt with exotic fruit or milk pudding with a swirl of chocolate. Sweet desserts and speciality yoghurts from Campina are what foodies reach for throughout the day. A tasty snack, with hygienic packaging.
Campina at Gütersloh produces a whole range of dairy products. The raw material here is milk. It can be processed as plain milk for drinking, mixed milk drinks, yoghurts and desserts as well as products made of cheese, butter and cream. The company regularly adds new specialities to its range: yoghurt with stracciatella, multi-flavoured “swirled” desserts, rice pudding with cherries with small portions in divided containers, which are filled separately. This international dairy producer never stops thinking up new ideas for the retail sector to make sure consumers are met with a wide selection of products in the chilled cabinet.
This often involves quickly switching between products at the factory, something that is of course only possible with sophisticated process technology and high logistical efficiency. Tankers containing fresh milk for the dairy products constantly roll up at Gütersloh. Other deliveries include ingredients such as fruit pulp, processed fruit, chocolate chips, cream or sweet woodruff, as well as containers of all shapes and sizes, already equipped with labels for the different brands. There are of course also boxes, which are then put together as crates on pallets for shipment. Every day between 1,200 and 1,500 pallets leave the factory laden with their delicious cargo, ready for distribution throughout Europe.
Blended in the container
Anyone walking through the production plant will be struck by the confusion of pipes containing brown, red or white liquids: chocolate pudding, fruit sauce or cream, which is conveyed via the filling system from the storage tanks to the containers standing ready. A sophisticated system of hose lines brings together the different ingredients in the filling machine and then blends them in the container. Three feed lines are required if chocolate pudding is to be swirled with vanilla pudding and then topped with cream. The heads of the filling machine accompany the containers on the conveyor belt and distribute the exact quantity of product required into each container via flexible PTFE corrugated hoses. In an unflagging one-second rhythm the hoses are moved along in step with the containers and then returned to their home position. One glance at the transparent hoses is all it takes for the plant foreman to tell whether it is cream, chocolate pudding, fruit yoghurt or vanilla sauce that is currently coursing through the pipes. This means he always has full control of the system to ensure a smooth product supply. One filling system can handle 28,000 containers per hour, generally operating in a cycle of 36 hours. The machine is then cleaned automatically and switched over to a new product.
Line engineering plays a key role at the company. Things are of course rather tight at the filling machines. To fill a crate with twelve 500 gr containers for example, the feed lines for the ingredients have to be connected to the relevant filling heads. Special pipes were once used for this purpose. This resulted in awkward situations as they sometimes had to be bent into complicated shapes to fit into the confined space available. Great accuracy was required to compensate for the slight deformation involved. Fast and flexible changeover of the production machinery was difficult due to the time-consuming process necessary here.
The solution: PTFE
Rainer Kahmann, the manager of the technical warehouse at Campina and Christian Koschorreck, responsible for engineering at Campina, consulted Mehmet Susever, MD of nautical elements. For 17 years he has assisted Campina with process technology at the plant in the role of an external service-provider. All three started looking for alternative solutions and came across HANSA‑FLEX Boffzen, the specialists for metal and PTFE hoses. Such hoses were absolutely ideal for Campina’s requirements. They joined forces to come up with the very best solutions – so immediately presenting the specialists from Boffzen with an enormous challenge.
“But HANSA‑FLEX proved to be very patient and always responded quickly,” said Mehmet Susever, who is still delighted about their cooperation. “And even at the weekend we didn’t hesitate to commission HANSA‑FLEX with the production of hoses. As the plant works non-stop, this meant we had to make use of the tight time slots available when the machines were being cleaned and prepared for new campaigns.” The specialists in Boffzen have proved themselves to be committed partners to Campina, something that has remained unchanged today. “HANSA‑FLEX is always at the end of the supply chain in terms of process technology – in other words, we can only determine the exact measurements for the PTFE hoses once a process line has been converted,” remarked Mehmet Susever. “But very fast delivery is then required. We order the hoses by phone, and they’re available just a few hours later.”
One by one the connecting pipes to the filling heads have now been replaced by transparent PTFE corrugated hoses, which are ideal for areas with high hygiene requirements. They have the advantage of being not only temperature-resistant but also odourless and tasteless – in other words, safe for use with foods. Compared with conventional industrial hoses, they greatly improve product quality, are easy to maintain and provide for CIP (cleaning-in-place) processes. In addition, PTFE hoses do not include metal parts. This is important for product safety: no metal particles can get into the containers.
One special advantage of PTFE hoses is of course their flexibility, which caters for minor variations in dimensions. They offer the necessary flexibility so that at filling plants, the feed lines can be quickly connected to the filling heads. Campina can thus achieve a significant reduction in set-up times and process costs.
At a plant that continuously manufactures fresh dairy products unscheduled downtimes should never last very long. This is why Rainer Kahmann, as the manager of the technical warehouse, has localised all key spare parts and keeps sufficient stocks of these components. Including of course a small supply of PTFE hose lines, articles which really only become unusable due to improper handling or mechanical influences. To avoid such influences Campina also uses PTFE hoses in areas where filling does not take place. These hoses feature a metal braid jacket or are protected from abrasion through contact with the ground by double metal spirals.
Learn more
- 12.03.2024
The world’s most powerful industrial blower
Aerzener Maschinenfabrik produces the most powerful positive displacement blower in the world currently. Power units from Willmann ensure smooth operation of the blowers - even under explosive ambient conditions.Find out more - 12.03.2024
A real challenge
HANSA-FLEX is a Zeppelin service partner for Cat construction machinery and enginesFind out more