Aerzener Maschinenfabrik produces the most powerful positive displacement blower in the world currently. Power units from Willmann ensure smooth operation of the blowers – even under explosive ambient conditions.
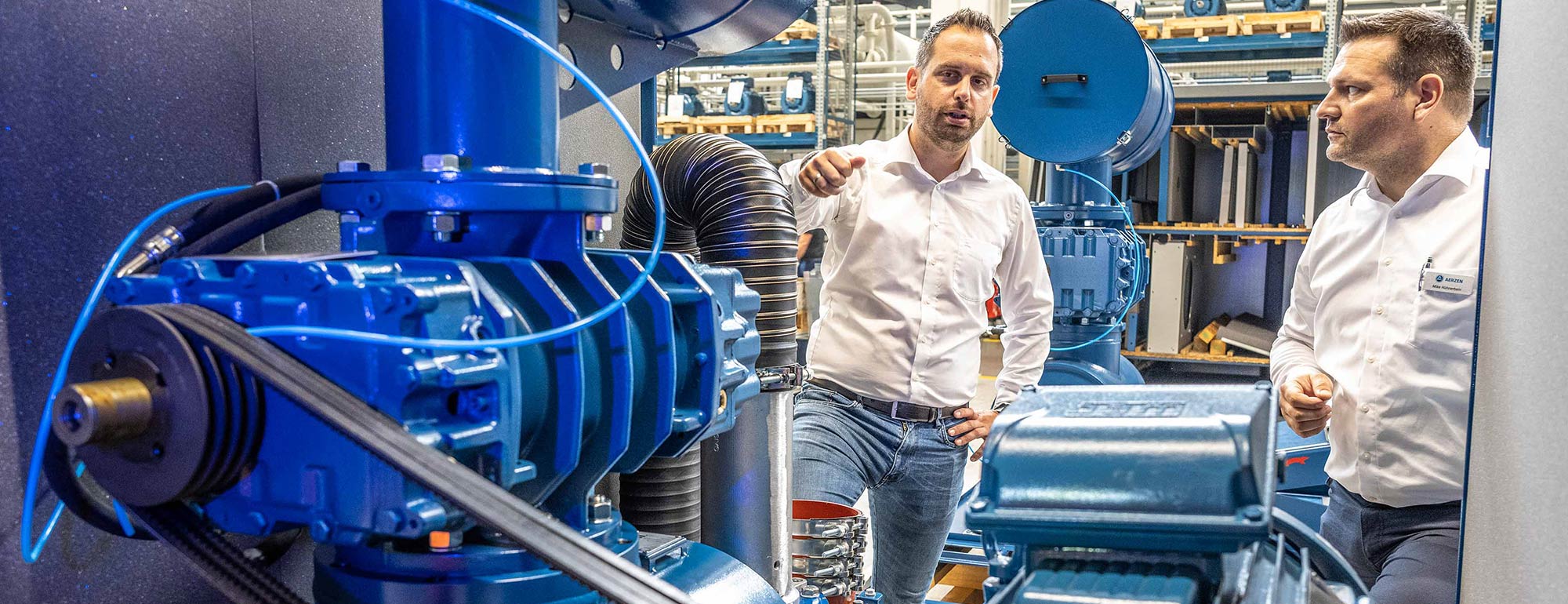
12.03.2024
The world’s most powerful industrial blower
Whether it’s chemical and process engineering, the steel industry and mining, the food industry, water and waste water treatment or even maritime applications: wherever air and gases have to be compressed or conveyed, the high-performance blowers and compressors from Aerzener Maschinenfabrik come into their own. Power units from Willmann Steuerungstechnik GmbH, a subsidiary of HANSAFLEX AG, ensure that the bearings of the blowers always receive the right amount of lubricant.
With an output of up to 77,000 m³/h the Alpha Blower is Aerzener Maschinenfabrik’s most powerful product. The rotary blower represents performance, reliability and efficiency to an equal degree. “In view of rising energy costs, our customers are increasingly looking at the total cost of a machine over its entire productive life. In very energy-intensive applications our products sometimes pay for themselves in less than a year”, explains Mike Hühnerbein, strategic purchaser at Aerzener Maschinenfabrik. In order for the Alpha Blower to be able to deliver its performance in continuous operation for many years, the continuous lubrication of its moving parts is essential. The oil supply is provided by power units from HANSA‑FLEX subsidiary Willmann Steuerungstechnik GmbH. They ensure that the right amount of oil is always in the right place at the right time. The design and construction of the individually manufactured power units was carried out in close cooperation with the customer. “With 24/7 operation our customers expect the highest standards from our machines. We are delighted that Willmann, just like us, attaches the greatest importance to quality and reliability.” For Hühnerbein, this includes not only manufacturing and documentation, but also consideration of a wide range of environmental conditions.
Explosive surroundings
Steelworks all over the world rely on blowers from Aerzener Maschinenfabrik to ventilate their blast furnaces. Continuous explosion protection of the systems is indispensable. Even a spark or heated parts of the equipment are enough to cause coal dust to react with oxygen and cause serious dust explosions. The power units produced by Willmann therefore comply with the strict ATEX directives of the European Union on explosion protection for equipment and machines in hazardous environments. In addition to the selection of appropriate components such as motors and pumps, welding processes and painting also have to be carried out in an explosion-proof manner. “Willmann bears great responsibility here, as error-free work is essential. However, the team has mastered this demanding task with ease,” explains Hühnerbein.
Straight to the production line
In addition to the power units for the oil supply, Aerzener Maschinenfabrik installs a number of components from HANSA‑FLEX. The spectrum ranges from screwed connections via hose lines and pipelines to pressure gauges. The components are supplied as kits straight to the production line. “The kits save time, as we can dispense with order picking in the operations planning department. With our synchronised production and high capacity utilisation, this is a real advantage,” comments Hühnerbein. Ready-made assemblies go one step further. Here HANSA‑FLEX assumes responsibility for the assembly of components. “The system partnership with HANSA‑FLEX enables a number of solutions that smaller suppliers can’t offer at all,” says Hühnerbein.
Fast maintenance
It is not least the high level of capacity utilisation that makes smooth production indispensable for Aerzener Maschinenfabrik. Proximity to the HANSA‑FLEX Hamelin branch guarantees short response times when hydraulic hose lines need to be replaced quickly. Smaller jobs are carried out by HANSA‑FLEX’s mobile Rapid Hydraulic Service. During official health and safety inspections and the regular replacement of a large number of hydraulic hoses, HANSA‑FLEX’s Industrial Service has several technicians on site at the customer’s premises. Particularly helpful is the fact that all the information on the hydraulic hose lines used is recorded in the My HANSA‑FLEX hose management portal – including maintenance intervals, inspection dates and allocation to the relevant machines. Looking back, Hühnerbein states: “The extremely positive experiences we had in maintenance operations were the deciding factor for us when it came to extending the cooperation to other areas and aiming for a strategic partnership.”
Cooperation based on partnership
What started with the supply of individual hydraulic hose lines has therefore developed into a close cooperation based on partnership. The proactive suggestions for the optimisation of components and assemblies are particularly appreciated by Aerzener Maschinenfabrik. “We are specialists in mechanical engineering, not in hydraulics”, comments Hühnerbein. For the purchasing specialist it is crucial to be able to fall back on an existing product portfolio and the large network of experts within HANSA‑FLEX at any time. “There is always a competent contact person available, even for complex questions. The fact that all enquiries are coordinated centrally via our HANSA‑FLEX customer advisor Daniel Sprenger is a further service to us.”
Learn more
- 11.03.2024
Clean oil, clean cement production
How Holcim turns a by-product of pig iron production into a valuable raw material for cement production, and why clean hydraulic oil is indispensable.Find out more - 12.03.2024
Fullest confidence throughout Europe
Boels Rental relies on the fast reactions of the Rapid Hydraulic ServiceFind out more - 12.03.2024
Non-stop operation
The self-discharging freight train of Havelländische Eisenbahn AGFind out more