Plannerer Holding AG relies on cooperation with HANSA-FLEX to optimise the 30-metre excavator arm
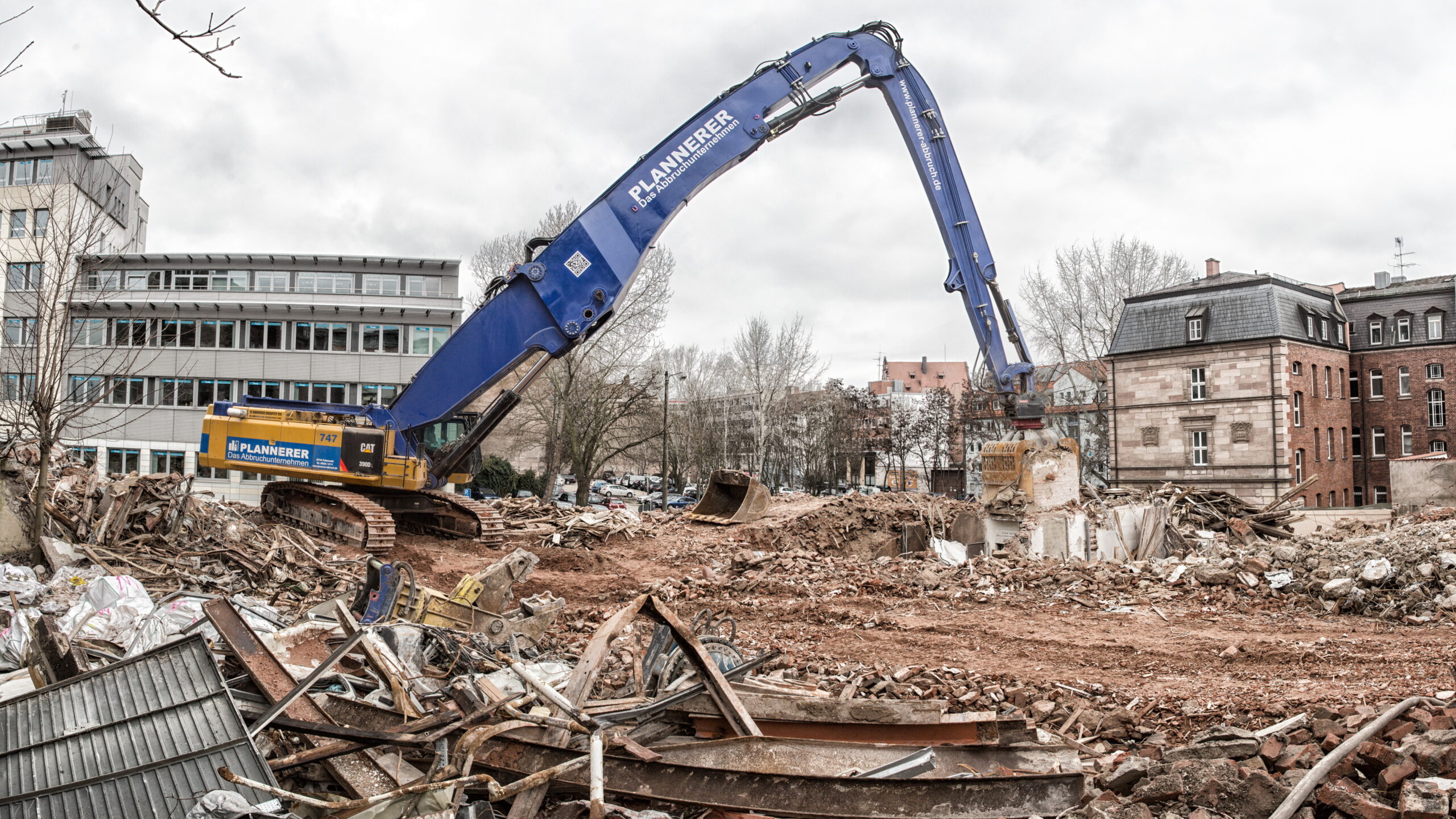
12.03.2024
A demolition giant in action
The BHD-3010 demolition boom with a reach height of 30 metres precisely and powerfully moves the demolition shears up to the façade of a house. Piece by piece, it carefully removes the solid concrete from the building and cuts through the reinforcement steel. Soon, all that remains of the building are piles of sorted rubble. The innovative excavator arm from Plannerer Holding KG has a far greater load capacity than conventional demolition excavators. The newly developed product speeds up demolition work and construction processes and reduces costs.
With a modern fleet of some 300 vehicles, Plannerer is one of Germany’s largest and Europe’s most innovative demolition companies. For more than 20 years, the company has specialised in demolition work, controlled dismantling, contaminated site remediation, decontamination and recycling. It furthermore leases construction machinery and caterpillar cranes.
The fleet was recently expanded to include a very special vehicle: a CAT390 excavator with a 30-metre long demolition boom. The innovative machine modification was designed and realised by BURDE Engineering GmbH. “Intricate ways to improve the demolition excavator only become evident once it is used on a construction site. In working with HANSA‑FLEX, we are supported by a partner that enables us to make full use of the arm’s potential”, reports Stephan Plannerer, Managing Director of Plannerer.
“With the customer portal, we can track exactly which hose was installed where and when. This gives us information about heavily stressed parts and at the same time enables us to optimise individual components.”
Stephan Plannerer
Managing Director of Plannerer
Perfect advice
Better performance can often be achieved through enhancements to minor details: “Too many threaded fittings and brackets are often not ideal for the flow. We recommended that Plannerer use pipe bends and had these produced by our pipe-bending centre in Schönebeck”, comments Ronny Kleber, commercial advisor at the HANSA‑FLEX office in Bayreuth. Plannerer was then able to directly install the parts on site.
HANSA‑FLEX also produces components for the demolition company that are otherwise difficult to obtain on the market and associated with very long lead times. “We urgently required special threaded fitting adapters. HANSA‑FLEX was quickly able to assist us”, commented Plannerer. The two companies are connected by long-standing business relations. “When Plannerer calls us up to ask for advice, we coordinate everything from Bayreuth so as to find an optimum solution”, reports Ronny Kleber. To this end, the office not only works in close cooperation with the pipe-bending centre but also with the special tube and fittings production department in Dresden and the sealing technology department in Königshofen.
Designed for major forces
The BDH-3010 excavator weighs 146 tonnes. This makes it possible to use demolition attachments weighing up to 10 tonnes. The hydraulics must be precisely tailored to this operating weight. After all, from the chain drive to the pivoting of the body to the movement of the excavator arm: every movement of the demolition giant is hydraulically activated. The pipes and hoses on the excavator are correspondingly large. They have a diameter of between 1¼ and 1½ inches so that a great volume can be pumped through the hydraulic system.
The HANSA‑FLEX office in Bayreuth has the necessary machinery to produce lines like these. A hydraulic press with 380 tonnes of compressive strength connects hoses and fittings that can later withstand the high peak pressure of 500 bar.
A clear overview of all components
To maintain a clear overview of the hydraulic parts, Plannerer uses the My.HANSA‑FLEX customer portal. “The customer portal enables us to precisely track which hose has been installed where and when. This not only provides us with information about parts subject to extreme stresses and strains but also enables us to optimise individual components”, explains Plannerer. The idea is therefore to record the entire excavator in My.HANSA‑FLEX. This should speed up maintenance and the replacement of individual components.
The HANSA‑FLEX office in Bayreuth always has important spare parts in stock so it can supply Plannerer as quickly as possible. “We also intend to fill a container in the immediate vicinity of the demolition excavator with spare parts. If a part fails, this can then be directly replaced, thereby minimising the excavator downtime and the resultant downtime costs”, reports Kleber. If necessary, the HANSA‑FLEX mobile hydraulic service also provides further assistance.
Always on hand
The excavator’s demanding area of use poses a major challenge in terms of technology and hydraulics: the BHD-3010 with the 30-metre arm had to be precisely optimised for huge loads. The hydraulics expert was able to provide advice on hoses that did not function satisfyingly under the high level of strain. “HANSA‑FLEX recommended that we use the HD800 hose, which is more flexible and suitable for higher pressures” reports Plannerer.
Plannerer intends to construct a telescopic demolition arm with a length of 65 metres; a 46-metre version has already been created for the BHD-3010. HANSA‑FLEX is also advising the demolition company in this regard and recommending components and materials. “In HANSA‑FLEX, we have found a hard-working partner who provides us with professional support in all hydraulics matters”, summarises Plannerer.
Learn more
- 12.03.2024
Hunting for treasure
Electrocycling GmbH obtains valuable raw materials from electronic wasteFind out more - 12.03.2024
Restoration of a loading giant
HANSA-FLEX repairs the cylinder on a 100-tonne crane for Lübecker Hafen-GesellschaftFind out more - 12.03.2024
Carved from a very special wood
Since the founding of the Pfeiffer Group's timber plant in Lauterbach in 2009, HANSA-FLEX has been the first point of contact there when it comes to hydraulics and the associated services.Find out more