With its mobile Quadriga platform the M-Group is revolutionising the maintenance of brickwork in industrial furnaces: a remote-controlled robot with a hydraulic hammer carries out previously manual damage-repair work more safely and cost-effectively.
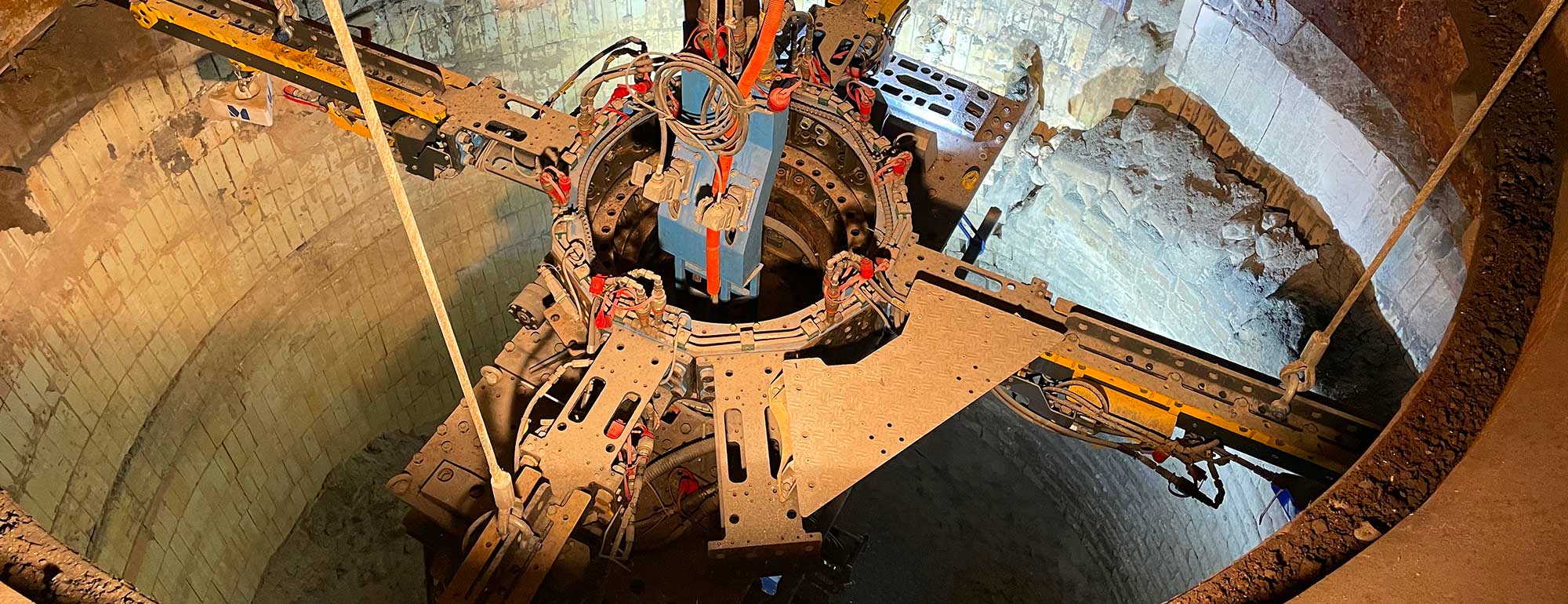
12.03.2024
A digital revolution in industrial operations
The brickwork of industrial furnaces needs to be repaired on a regular basis. With its globally unique Quadriga mobile platform, the M-Group has succeeded for the first time in combining the competing goals of workplace safety, time savings, cost reduction and process optimisation.
As different as cement, steel, glass, aluminium or even sugar may seem at first glance, they have one central factor in common: industrial furnaces are essential for their production. Temperatures of well over 1,000 °C are commonplace. For example, a temperature of 1,450 °C is required to burn cement. The furnaces are lined on the inside with fireproof brickwork to optimise heat effectiveness. The brick-lined sections reach diameters of up to 15 metres and heights of up to 100 metres.
Regular inspections and overhauls of industrial furnaces and, above all, their brickwork are mandatory: “During the production of cement, abrasion causes erosion of the fireproof lining. In addition, there are stresses caused by temperature changes and thermochemical corrosion, which leads to damage and flaking in the brickwork,” explains Bennet Röpke, Project Manager in charge of the development of the Quadriga at the M-Group. To maintain the brickwork, the plant operators or specialised service providers previously had to erect scaffolding inside the furnace. Deposits were then removed from the surface of the brickwork and damaged bricks were removed and replaced. This is physically demanding work which is not without danger for the specialised bricklayers due to poor visibility, high temperatures, falling bricks, dust and noise. It is also very time-consuming and costly. At a cement works, downtime costs of up to €200,000 can quickly arise – per day, it should be noted. Coordinating the various trades involved is another uncertainty factor.
Revolution instead of evolution
Describing the pressure behind the new development, Karen Maria Mönstermann from the company’s PR and Marketing section states: “There has been virtually no progress in this area in the last one hundred years. We therefore looked for a solution to simultaneously optimise the diametrically opposed factors of workplace safety, costs, time and process quality.” In the Quadriga, the M-Group has developed a solution that is not just an evolution, but a genuine revolution in the maintenance of industrial furnaces. The previously used scaffolding is replaced by a platform that moves vertically up and down inside the furnace on cables. Up to six hydraulic cylinders securely support the side of the platform. The time saved compared to conventional scaffolding is enormous: whereas its assembly and dismantling within a furnace used to take around 100 hours, the platform takes just 14 hours for the same purpose.
Digitalised operations
However, the innovation is not limited to replacing the scaffolding. With the Quadriga, a robot arm that can swivel and rotate in all directions with a hydraulically driven hammer performs the previously manual work of demolishing the masonry. The advantage is that the Quadriga pilot, who controls the robot arm, sits outside the furnace in a cabin that serves as a control centre. Multiple cameras, microphones and sensors maintain contact between the furnace and the control centre. “The digitalisation of maintenance work with the Quadriga platform not only increases safety at work, but also efficiency, as the robot arm can be used 24/7. At the same time we take the pressure off our employees and, not least, make our occupation more attractive to young people,” says Ms Mönstermann, summarising the benefits provided by Quadriga.
Decentralised hydraulics
To protect the hydraulic power pack from vibration and dust, it is located outside the furnace for easy maintenance. The supply and return lines are connected to the Quadriga platform via a triple hose reel with a length of 40 metres. The third hose transports compressed air for cleaning the cameras, but can also be used for the hydraulics in the event of problems. “For the hose reel we use the Pro hose lines from HANSA‑FLEX, which are many times more abrasion-resistant than standard hose lines thanks to their hardened plastic cover,” reports Röpke.
We formulate our requirements and HANSA‑FLEX quickly provides suggestions from which we can choose. This makes development easier and at the same time we receive valuable input.
Bennet Röpke
Project manager of the Quadriga
Personalised service
A large number of HANSA‑FLEX components are used in the Quadriga platform. Sometimes tight installation spaces require creative solutions in hydraulics, especially because the Quadriga needs to be transported in a space-saving manner, which is reflected in confined installation spaces. Röpke appreciates the proximity of the Lemgo branch and the personal contact: “We specify our requirements and HANSA‑FLEX quickly provides us with suggestions from which we can choose. This makes our development work easier, and at the same time we receive valuable ideas.” HANSA‑FLEX Account Manager Andre Dux is the central point of contact for the coordination between the branch, the Rapid Hydraulic Service, cylinder production, engineering and power pack construction as well as the HANSA‑FLEX subsidiary Willmann Steuerungstechnik. “We are proud to be supporting such a pioneering development and to be able to contribute our expertise from the most diverse areas of hydraulics,” says Dux.
Learn more
- 13.03.2024
Experience preventive maintenance up close: 360° industrial service
Have you ever wondered what our industrial service is all about and what services are hidden behind it?Find out more - 12.03.2024
Close proximity, short response times
BSH Hausgeräte benefits from the full-service offerFind out more - 12.03.2024
Efficient hose management
GKN benefits from seamless interaction between company and service providerFind out more