There is a hustle and bustle at the Cruise Center in Warnemünde. Families, couples and travel groups of all ages drag their suitcases behind them in anticipation and cast expectant glances at the cruise ship AIDAbella.
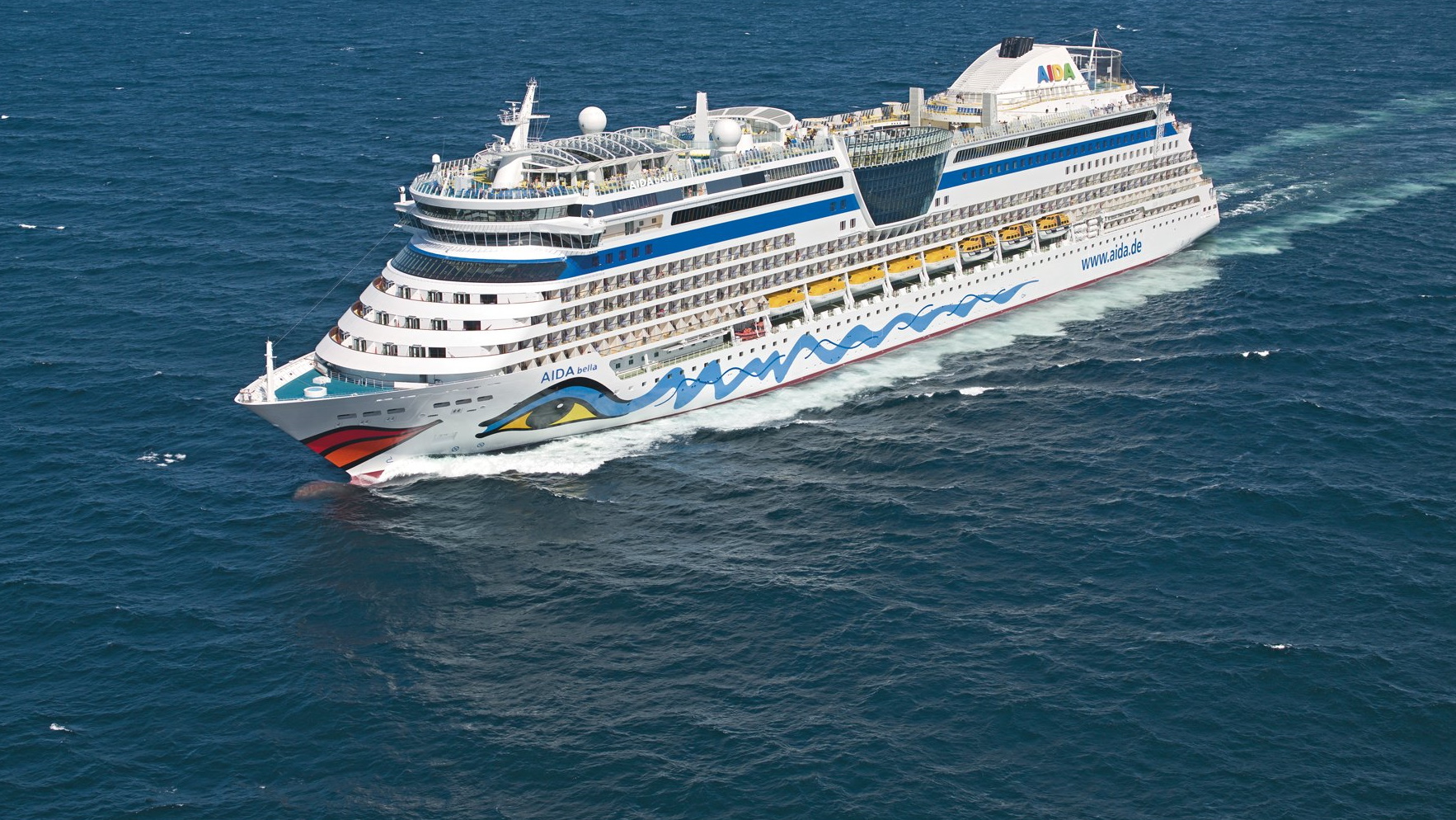
12.03.2024
Kissing the waves
The Cruise Centre in Warnemünde is a flurry of activity. Families, couples, and tour groups representing every age group eagerly pull their luggage along behind them and cast expectant glances at the cruise ship AIDAbella, lying at anchor in the Baltic Sea. The radiant sunshine and the salty sea air add their touch to the holiday mood that pervades the scene. We too would be delighted to move into one of the 1,025 guest cabins and head out to sea with the AIDAbella. But, alas, our brief on-board visit has a completely different purpose.
Music enthusiasts surely connect the name Aida with the opera of the same name by Giuseppi Verdi. For historians, the name may call to mind the ancient Egyptian Nubian princess. Astronomers likely think of the eponymous asteroid, and a very small group of keen geographers know that in Japan there is a small prefecture of Okayama that bears that name. But just about any German you ask connects the name with the cruise line AIDA Cruises and its cruise ships which bear the company name. This degree of name recognition is all the more notable considering that the cruise line founded in 1999 as Seetours International did not change its name to AIDA Cruises until 2004. Since then, the market leader among cruise lines in Germany has written a success story that is the envy of the industry.
Impressive figures
In 2012, 632,719 holidaymakers took a trip on one of the ten AIDA ships. This corresponds to around half of all Germans who set sail on an ocean cruise in the same year. In order to fulfil the high demand, the Rostock-based cruise operator put a new ship into service every year between 2007 and 2013, all of which were built at the Meyer shipyard in Papenburg. The fleet currently has a total capacity of 18,636 beds. But this is by no means the end of the story. In August 2011, AIDA Cruises announced that it had ordered two more newbuilds, which are due to enter service in 2015 and 2016. The ships will be built by Mitsubishi Heavy Industries in Japan and, at 300 metres long, 37.6 metres wide and 125,000 GT (gross tonnage), will be significantly larger than any other ship in the Kussmund fleet. For comparison: the AIDAbella we visited measures 69,203 GT.
All-inclusive cruise package
Size is not everything. People who spend their holidays aboard cruise ships also want to be entertained when not at ports of call. All of the AIDA ships go to great lengths to guarantee an all-round holiday experience. Guests on the AIDAbella are spoiled by culinary delights in seven restaurants and eleven bars, for instance. A huge sun deck with an array of swimming pools invites guests to relax, as does a broad range of wellness spa treatments. Sports fans can enjoy a workout in the gym, on the running track, or by taking part in one of the more than 30 different fitness courses. Life aboard ship is enhanced by an on-board library, a casino and a cinema. Young guests can play and have fun at the kids’ club. Nightly shows and musical events offer first-class entertainment. One thing is certain: passengers will not be bored.
Technical equipment on board
To ensure that the holiday fun is never spoiled, the machinery and equipment on board has to function smoothly at all times. The same goes for the hydraulic systems and hoses that are installed, inter alia, in the ship’s trash compactor, hatches, and engine room. Jan Miesenburg, the technical superintendent at AIDA Cruises, is responsible for ensuring smooth operations. Miesenburg is who we are visiting on board the AIDAbella. After we pass through the security check, he welcomes us aboard the ship to conduct the interview for this article. His top priority for the interview is speed. We have to finish up quickly because in just a few hours the AIDAbella will weigh anchor for its Baltic Sea cruise and Miesenburg has plenty to do before the dock lines are cast off.
Maintenance ensures safety
In the interview, it immediately becomes clear that system safety and availability are the top priorities for AIDA Cruises, which is why the technical superintendent takes the replacement intervals specified in German occupational safety regulation BGR 237 for hydraulic hose assemblies very seriously. “We completely replace all of the lines at every second maintenance phase in the shipyard – that is, every six years – unless, of course we see premature wear,” says Jan Miesenburg.
Since 2008, AIDA Cruises has repeatedly drawn on the products and services of HANSA‑FLEX AG. X-CODEs and the new customer portal my.hansa-flex have been a particular benefit for AIDA. “Now, every single hose line – and there are many, many on board – carries an X-CODE. In the future this will spare us the tedious task of measuring the hose lines. The customer portal also gives me an overview of all hoses that are built into the individual vessels. That makes it much easier to plan and implement maintenance intervals in advance,” the technical director explains.
The customer portal gives me an overview of all the hose lines installed in the individual ships. That it is immense to plan and implement maintenance intervals with foresight!
Jan Miesenburg
Technical Superintendent AIDA Cruises
Reliable partner
Another reason for cooperation with HANSA‑FLEX is global availability. In nearly every port of call where the ships of the AIDA fleet land, they find a branch office of the system supplier for hydraulics. “So, when in doubt, we always have quick access to spare parts,” says Miesenburg. But for him there is yet another reason for doing business with HANSA‑FLEX. “First and foremost, our suppliers have to be flexible and react quickly, because repairs and deliveries can often only be performed when the ships are in port, and that is sometimes just a brief period. The time in port can also fall on a weekend. In this regard, we have always had good experiences with HANSA‑FLEX,” says the AIDA employee. These statements bring a smile to Volker Hansen’s face. Hansen is head of the HANSA‑FLEX branch in Rostock. He coordinates all of the external operations originating in Rostock. The hose lines AIDA needs are assembled in the local branches and delivered directly to the ship. Germanischer Lloyd approved hose assemlies are produced by employees of the HANSA‑FLEX specialist hose production facility in Hamburg. From there they are sent directly to the job site.
Just 20 minutes after boarding, we leave the ship with a wistful glance at the tourists cheerfully boarding the AIDAbella. We, too, want to set off on the cruise. Not today. But our next holiday is not far off.
Learn more
- 12.03.2024
They launch whatever the weather
The men and women of the German Maritime Search and Rescue Service (DGzRS) experience emergencies a good 2,000 times a year. They go out to sea to help people in distress. Day and night, wind and weather, summer and winter.Find out more - 12.03.2024
Keeping the world in motion
Just a stone’s throw away from Hamburg airport is a city within the city – the head office of Lufthansa Technik AG. HANSA-FLEX supplies a large number of products, including several that are incorporated into the test benches.Find out more